Kärcher
ZUVERLÄSSIGE STROMVERSORGUNG DURCH INTELLIGENTES BATTERIEMANAGEMENT
INDUSTRY
Manufacturing
CLOUD PROVIDER
Other
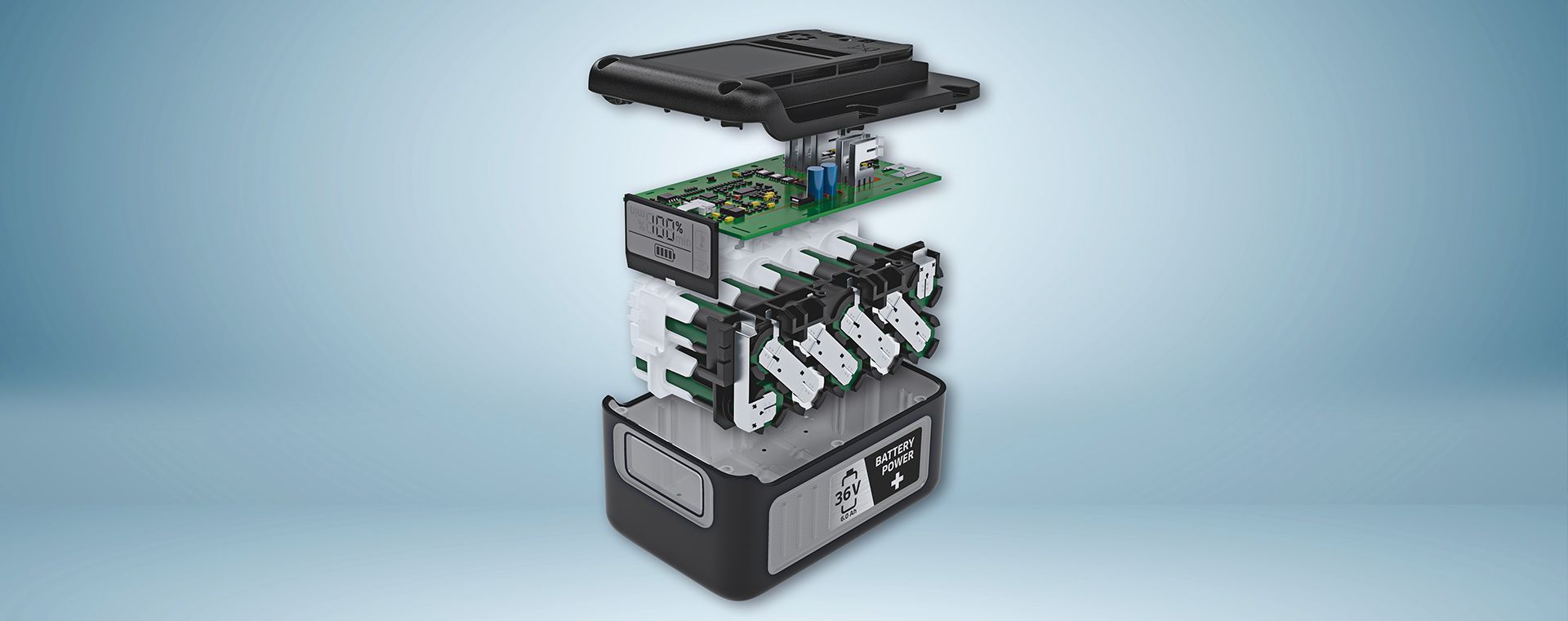
Um einen batteriebetriebenen Roboter zu entwickeln, bei welchem die Akkus im laufenden Betrieb gewechselt und Arbeitsunterbrechungen so möglichst vermieden werden können, benötigte Kärcher ein spezielles Batteriemanagement-System. Zoi und Kärcher entwickelten die Lösung gemeinsam von der Anforderungsanalyse bis hin zur industriellen Serienproduktion.
This is a paragraph. Writing in paragraphs lets visitors find what they are looking for quickly and easily.
This is a paragraph. Writing in paragraphs lets visitors find what they are looking for quickly and easily.
This is a paragraph. Writing in paragraphs lets visitors find what they are looking for quickly and easily.
This is a paragraph. Writing in paragraphs lets visitors find what they are looking for quickly and easily.
ROBOTERBETRIEB OHNE UNTERBRECHUNGEN
2 AKKUS MIT SCHUTZSCHALTUNG ZUR VERMEIDUNG VON SYSTEMAUSFÄLLEN
BEREIT FÜR DIE INDUSTRIELLE SERIENPRODUKTION
EIN BATTERIEMANAGEMENT-SYSTEM MIT HOT SWAPPING-FUNKTION
Kärcher stand vor einer kniffligen Herausforderung: Die Entwicklung eines kabellosen Roboters, der ohne Unterbrechung arbeiten konnte. Die Lösung? Ein batteriebetriebener Alleskönner, bei dem es selbst während des Einsatzes möglich ist die Akkus zu wechseln. Doch das war einfacher gesagt als getan. Für die Realisierung arbeitete Kärcher eng mit Zoi zusammen, um ein bahnbrechendes Batteriemanagement-System (BMS) zu entwickeln. Der Roboter sollte nicht nur Hot Swapping-fähig sein, sondern auch die Akkus der Kärcher Akku Plattform unterstützen.
Der Mikrocontroller auf dem BMS wurde wiederum über ein Bussystem mit dem Prozessor des Roboters verbunden. Dadurch kann der Prozessor die Ladezustände der Akkus, Ladeströme und weitere Systemzustände des BMS abrufen und weiterverarbeiten.
Nachdem das Konzept für das BMS feststand, wurden der Stromlaufplan und die Leiterplatte entworfen. Dabei war es wichtig, eine Leiterplatte zu konstruieren, die aufgrund der Miniaturisierung in der Lage ist, thermische Energie abzuleiten.
Ein Fokus lag von Anfang an auf der Serienfertigung der Baugruppe. Aus diesem Grund wurden die Bauteile so platziert, dass eine Fertigung mit geringer Fehlerrate möglich war. Außerdem wurde die Baugruppe so entwickelt, dass ein End-Of-Line-Test während der Produktion effizient durchgeführt werden kann.
Nach Fertigstellung des CAD-Modells der Leiterplatte konnten wir diese erfolgreich bei einem EMS-Dienstleister, mit dem wir seit mehreren Jahren eng zusammenarbeiten, fertigen lassen.
Um die Funktionalität der Baugruppe nachzuweisen, sind wir in zwei Schritten vorgegangen. Im ersten Schritt haben wir die Baugruppe in unserer Klimakammer getestet. Ziel dieser Tests war es, nachzuweisen, dass die Baugruppe unter den spezifizierten klimatischen Bedingungen fehlerfrei funktioniert. Außerdem haben wir über mehrere Temperaturzyklen hinweg nachgewiesen, dass thermische Veränderungen in der Umgebung keine mechanischen Defekte an der Baugruppe verursachen.
Neben den thermischen Tests folgte ein Dauerlauf für die Baugruppe. Hierfür konstruierten wir ein Hardware-In-The-Loop-Prüfsystem, das die Hardware und Firmware des Batteriemanagement-Systems über einen definierten Zeitraum rund um die Uhr testete.

Während der Tests wurden die Akkus kontinuierlich geladen und entladen. Hierzu verwendeten wir programmierbare elektronische Lasten, um das Zielsystem des Roboters in seiner elektronischen Last zu simulieren. Entladeströme, die beispielsweise durch eingeschaltete Antriebe und Sensoren entstehen, wurden nachgebildet. Weiterhin wurden die Akkus durch programmierbare Netzteile simuliert, um die Baugruppe an die spezifizierten Grenzwerte zu bringen.
Letztendlich konnte das BMS alle Anforderungen erfüllen, die im initialen Requirements-Workshop festgelegt wurden.
VON DER ANFORDERUNGSANALYSE BIS ZUR INDUSTRIALISIERUNG
Um die funktionalen und nicht funktionalen Anforderungen an das System im Detail zu ermitteln, führten wir mehrere Workshops mit Kärcher durch. Darauf basierend wurde das Konzept für das BMS mit zwei Hot Swap-fähigen Akkus erstellt. Dabei haben wir nicht nur alle elektrotechnischen und elektromechanischen Komponenten ausgewählt, sondern auch die mechanischen Dimensionen der Leiterplatte konzipiert.
Das Konzept wurde in einen Stromlaufplan umgewandelt und die Leiterplattenentflechtung durchgeführt. Anschließend übergaben wir die CAD-Daten an einen EMS-Dienstleister, um einen funktionsfähigen Prototypen herzustellen. Der Prototyp wurde ausgiebig auf seine Funktionalität getestet – u. a. mit Tests in unserer Klimakammer sowie in einem eigens entwickelten Hardware-In-The-Loop-Testsystem.
Da unser Fokus auf der Serienproduktion des BMS lag, unterstützten wir den Kunden von der Anforderungsanalyse über die Entwicklung bis hin zur Industrialisierung des Systems.

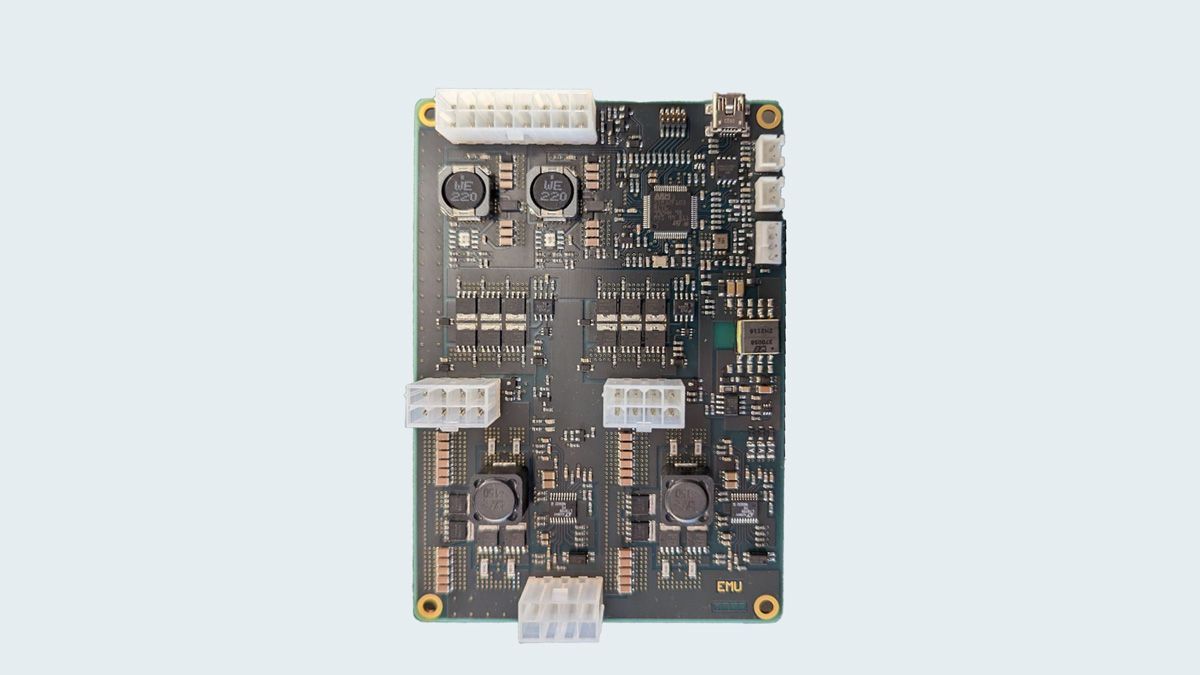
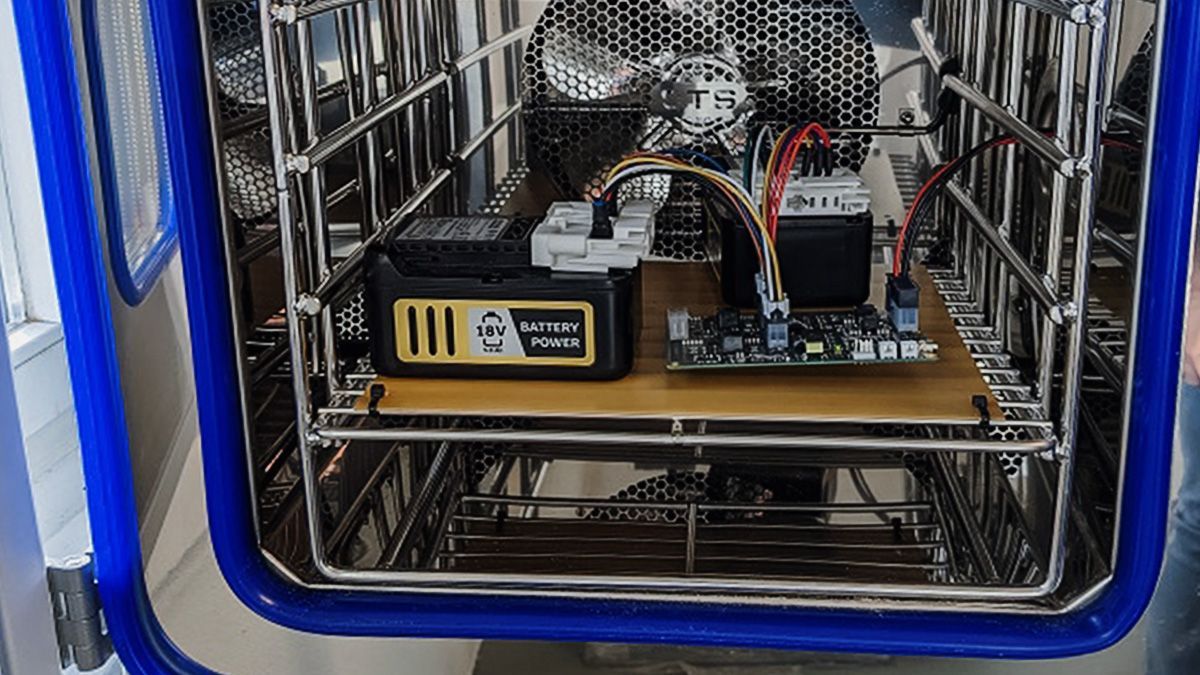
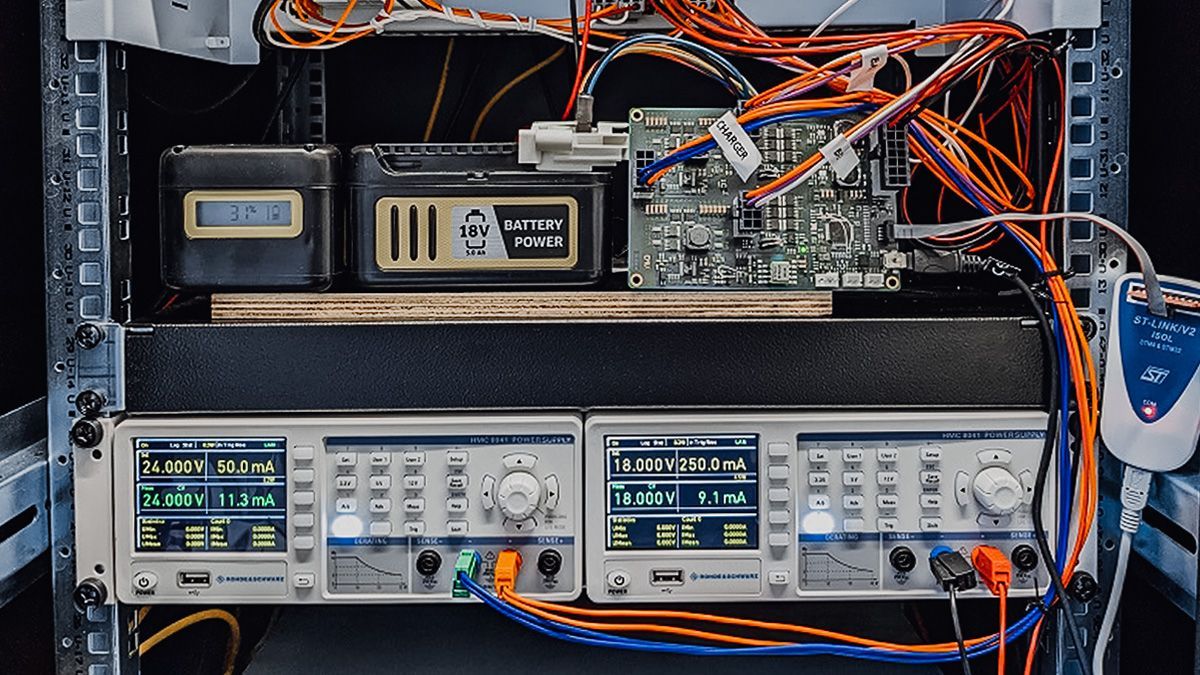
MIKROCONTROLLER PRÜFEN LADESTÄNDE UND STEUERN DEN STROMFLUSS
Die Funktionalität des BMS besteht aus zwei Akkus, die ihre Systemzustände selbständig durch einen integrierten Mikrocontroller überwachen und die so gewonnenen Systeminformationen über ein Bus-System mitteilen. Der im Batteriemanagement befindliche Mikrocontroller kann so jederzeit die Systemzustände beider Akkus abfragen und verarbeiten, wie beispielsweise den Ladestand, um die korrekten Ladeströme anzulegen.
Um die elektrische Energie der beiden Akkus in den Roboter übertragen zu können, wurde ein Hot Swap Controller ins BMS integriert. Dieser hat die Aufgabe, die elektrische Energie der einzelnen Akkus zu entnehmen. Wenn ein Akku entfernt wird, muss der Hot Swap Controller auf den anderen, noch im System vorhandenen Akku umgestellt werden.
Die eigentliche Herausforderung bei der Entwicklung des Hot Swap Controllers bestand darin, dass die zum Einsatz kommenden Akkus aus der Kärcher Akku Plattform eine eigene Schutzbeschaltung aufweisen. Das Zusammenspiel dieser Schutzschaltung mit dem Hot Swap Controller erforderte viel Entwicklungsaufwand, um beide Systeme aufeinander abzustimmen.
Die Funktionalität des BMS ist in diesem Blockschaltbild visualisiert.
Das CAD-Modell der Leiterplatte.
Die thermischen Tests in der Klimakammer sollten sicherstellen, dass die Baugruppe einwandfrei funktioniert.
Das Hardware-In-The-Loop-Prüfsystem testete die Hardware und Firmware des BMS ununterbrochen über einen definierten Zeitraum.
Die fertiggestellte Leiterplatte.
ÜBER KÄRCHER
Die Alfred Kärcher SE & Co. KG mit Sitz in Winnenden und 150 Tochtergesellschaften in 78 Ländern ist der weltweit führende Anbieter von Reinigungstechnik. Für seine innovative Service- und Produktpalette, insbesondere die Kärcher Hochdruckreiniger, erlangte der Konzern internationale Bekanntheit in sämtlichen Bereichen der professionellen Reinigung. Das Familienunternehmen beschäftigt mehr als 14.400 Mitarbeiterinnen und Mitarbeiter und kann auf eine über 85-jährige Firmengeschichte zurückblicken.
CAROUSEL FILTER SETUP
CASES
Hier sind einige Beispiele, wie wir unsere Kunden aus der herstellenden Industrie erfolgreich unterstützt haben.
This is a paragraph. Writing in paragraphs lets visitors find what they are looking for quickly and easily.
This is a paragraph. Writing in paragraphs lets visitors find what they are looking for quickly and easily.
This is a paragraph. Writing in paragraphs lets visitors find what they are looking for quickly and easily.
This is a paragraph. Writing in paragraphs lets visitors find what they are looking for quickly and easily.
LET’S EXCHANGE IDEAS
Denn Sie könnten viel schneller die Richtung ändern, als Sie denken.